Металлдын катуулугунун коду H. Катуулуктун ар кандай сыноо ыкмаларына ылайык, шарттуу өкүлчүлүктөргө Brinell (HB), Rockwell (HRC), Vickers (HV), Leeb (HL), Shore (HS) катуулук ж.б. кирет, алардын арасында HB жана HRC көбүрөөк колдонулат. HB колдонуунун кеңири спектрине ээ жана HRC жогорку беттик катуулугу бар материалдар үчүн ылайыктуу, мисалы, жылуулук менен иштетүүнүн катуулугу. Айырмачылыгы, катуулугун текшергичтин индентери башка. Бринеллдин катуулугун өлчөөчү аспап шарды интентер, ал эми Роквелл катуулугун текшерүүчү алмазды индентер.
HV-микроскоп менен анализдөө үчүн ылайыктуу. Vickers катуулугу (HV) 120kg кем жүк жана 136 ° чокусу бурчу менен алмаз чарчы конус индентер менен материалдын бетин басыңыз. Материалдык чегинүү чуңкурунун бетинин аянты жүктүн маанисине бөлүнөт, ал Викерс катуулугунун мааниси (HV). Vickers катуулугу HV катары көрсөтүлөт (GB/T4340-1999 карагыла) жана ал өтө жука үлгүлөрдү өлчөйт.
HL портативдик катуулугун текшерүүчү өлчөө үчүн ыңгайлуу. Катуулуктун бетине сокку уруу жана секирүү үчүн сокку шарынын башын колдонот. Катуулугу үлгүнүн бетинен 1 мм аралыкта соккунун кайра көтөрүлүү ылдамдыгынын сокку ылдамдыгына карата катышы менен эсептелет. Формула: Либ катуулугу HL=1000×VB (кайра көтөрүлүү ылдамдыгы)/VA (таасир ылдамдыгы).
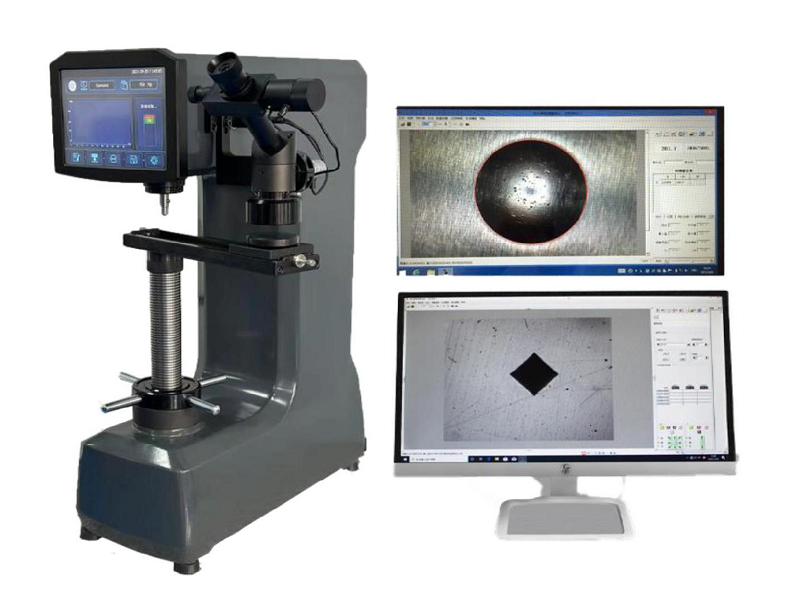
Portable Leeb катуулугун текшерүүчү Brinell (HB), Rockwell (HRC), Vickers (HV), Shore (HS) катуулугун Leeb (HL) өлчөө кийин айландырылат болот. Же Brinell (HB), Rockwell (HRC), Vickers (HV), Leeb (HL), Shore (HS) менен катуулуктун маанисин түздөн-түз өлчөө үчүн Либ принцибин колдонуңуз.
HB - Brinell катуулугу:
Brinell катуулугу (HB) көбүнчө материал жумшак болгондо колдонулат, мисалы, түстүү металлдар, болот термикалык иштетүүгө чейин же күйдүрүүдөн кийин. Рокуэллдин катуулугу (HRC) көбүнчө катуулугу жогору болгон материалдар үчүн колдонулат, мисалы, жылуулук менен дарылоодон кийинки катуулук ж.б.
Brinell катуулугу (HB) белгилүү бир өлчөмдөгү сыноо жүк болуп саналат. Сыноо үчүн металлдын бетине катууланган болот шары же белгилүү диаметрдеги карбид шары басылган. Сыноо жүктөмү белгиленген убакытка чейин сакталат, андан кийин сыналуучу беттеги оюктун диаметрин өлчөө үчүн жүк алынып салынат. Бринеллдин катуулугунун мааниси жүктү оюктун сфералык бетинин аянтына бөлүүдөн алынган коэффициент. Жалпысынан алганда, белгилүү бир өлчөмдөгү (көбүнчө диаметри 10 мм) катууланган болот шары белгилүү бир жүк (көбүнчө 3000 кг) менен материалдын бетине басылып, белгилүү бир убакытка чейин сакталат. Жүк алынып салынгандан кийин, жүктүн чегинүү аянтына катышы Бринелдин катуулугунун мааниси (HB), ал эми бирдиги килограммдык күч/мм2 (Н/мм2) болуп саналат.
Роквеллдин катуулугу чегинүүнүн пластикалык деформациясынын тереңдигинин негизинде катуулуктун баалуулук индексин аныктайт. Катуулуктун бирдиги катары 0,002 мм колдонулат. HB>450 же үлгү өтө кичинекей болгондо, Brinell катуулугун текшерүүнү колдонууга болбойт жана анын ордуна Роквеллдин катуулугун өлчөө колдонулат. Белгилүү жүктүн астында сыналуучу материалдын бетине басуу үчүн чокусу 120° бурчтуу алмаз конус же диаметри 1,59 же 3,18 мм болгон болот шар колдонулат жана материалдын катуулугу оюктун тереңдигинен эсептелет. Сыноочу материалдын катуулугуна ылайык, ал үч түрдүү масштабда көрсөтүлөт:
HRA: Бул 60 кг жүктү жана бриллиант конус индентерди колдонуу менен алынган катуулук, ал өтө катуулугу (мисалы, цементтелген карбид ж.б.) материалдар үчүн колдонулат.
HRB: Бул 100 кг жүктү жана 1,58 мм диаметри менен катууланган болот шарды колдонуудан алынган катуулугу, ал төмөнкү катуулугу бар материалдарга (мисалы, күйдүрүлгөн болот, чоюн ж.б.) колдонулат.
HRC: Бул 150 кг жүк жана бриллиант конус индентер колдонуу менен алынган катуулугу, катуулугу абдан жогору материалдар үчүн колдонулат (мисалы, катууланган болот, ж.б.).
Кошумча:
1.HRC Rockwell катуулук C масштабын билдирет.
2.HRC жана HB өндүрүштө кеңири колдонулат.
3.HRC тиешелүү диапазону HRC 20-67, HB225-650 барабар,
Катуулугу бул диапазондон жогору болсо, Rockwell катуулук A шкаласын HRA колдонуңуз,
Катуулугу бул диапазондон төмөн болсо, Rockwell катуулук B шкаласын HRB колдонуңуз,
Brinell катуулугунун жогорку чеги HB650 болуп саналат, ал бул мааниден жогору болушу мүмкүн эмес.
4.Роквеллдин катуулугун текшергич C шкаласынын индентери 120 градус бурчу менен алмаз конус болуп саналат. Сыноо жүктөө белгилүү бир мааниге ээ. Кытай стандарты 150 кгф. Brinell катуулугун текшергичтин индентери катууланган болот шар (HBS) же карбид шары (HBW) болуп саналат. Сыноо жүктөмү шардын диаметрине жараша өзгөрүп турат, 3000ден 31,25 кгс чейин.
5.The Rockwell катуулук чегинүү абдан кичинекей, жана өлчөнгөн маани локалдаштыруу болуп саналат. Орточо маанини табуу үчүн бир нече пункттарды өлчөө керек. Ал даяр продукцияга жана жука кесимдерге ылайыктуу жана кыйратуучу сыноо катары классификацияланат. Brinell катуулук чегинүү чоңураак, өлчөнгөн маани так, ал даяр продукцияга жана жука кесимдерге ылайыктуу эмес жана көбүнчө кыйратуучу сыноо катары классификацияланбайт.
6. Роквеллдин катуулугунун катуулук мааниси бирдиксиз аты жок сан. (Ошондуктан, Роквеллдин катуулугун белгилүү бир даража деп айтуу туура эмес.) Бринеллдин катуулугунун катуулук мааниси бирдиктерге ээ жана тартылуу күчү менен белгилүү болжолдуу байланышка ээ.
7. Rockwell катуулугу түздөн-түз терүү же санарип көрсөтүлөт. Бул иштетүү үчүн жеңил, тез жана интуитивдик, жана массалык өндүрүш үчүн ылайыктуу. Бринелдин катуулугу чегинүү диаметрин өлчөө үчүн микроскопту талап кылат, андан кийин үстөлдү карап же эсептеп чыгууну талап кылат, аны иштетүү кыйыныраак.
8. Белгилүү шарттарда, HB жана HRC столду карап алмаштырылышы мүмкүн. Менталдык эсептөө формуласын болжол менен төмөнкүдөй жазса болот: 1HRC≈1/10HB.
Катуулугу сыноо механикалык касиет сыноодо жөнөкөй жана жеңил сыноо ыкмасы болуп саналат. Кээ бир механикалык касиет сыноолорду алмаштыруу үчүн катуулук сыноосун колдонуу үчүн, өндүрүштө катуулук менен күчтүн ортосундагы так конвертация мамилеси талап кылынат.
Металл материалдарынын ар кандай катуулугунун маанилеринин ортосунда жана катуулуктун мааниси менен бекемдиктин ортосунда болжолдуу тиешелүү байланыш бар экендигин практика далилдеди. Катуулуктун мааниси баштапкы пластикалык деформацияга туруштук берүү жана уланган пластикалык деформацияга каршылык менен аныкталат, анткени материалдын күчү канчалык жогору болсо, пластикалык деформацияга каршылык ошончолук жогору жана катуулугу ошончолук жогору болот.
Посттун убактысы: 16-август-2024